Urushi lacquer painting is a traditional technique that has been used since ancient times in Japan. Urushi lacquer is used not only for its beautiful gloss, but also for preliminary process for various techniques such as makie lacquer painting with gold powder, and applying gold leaf on products.
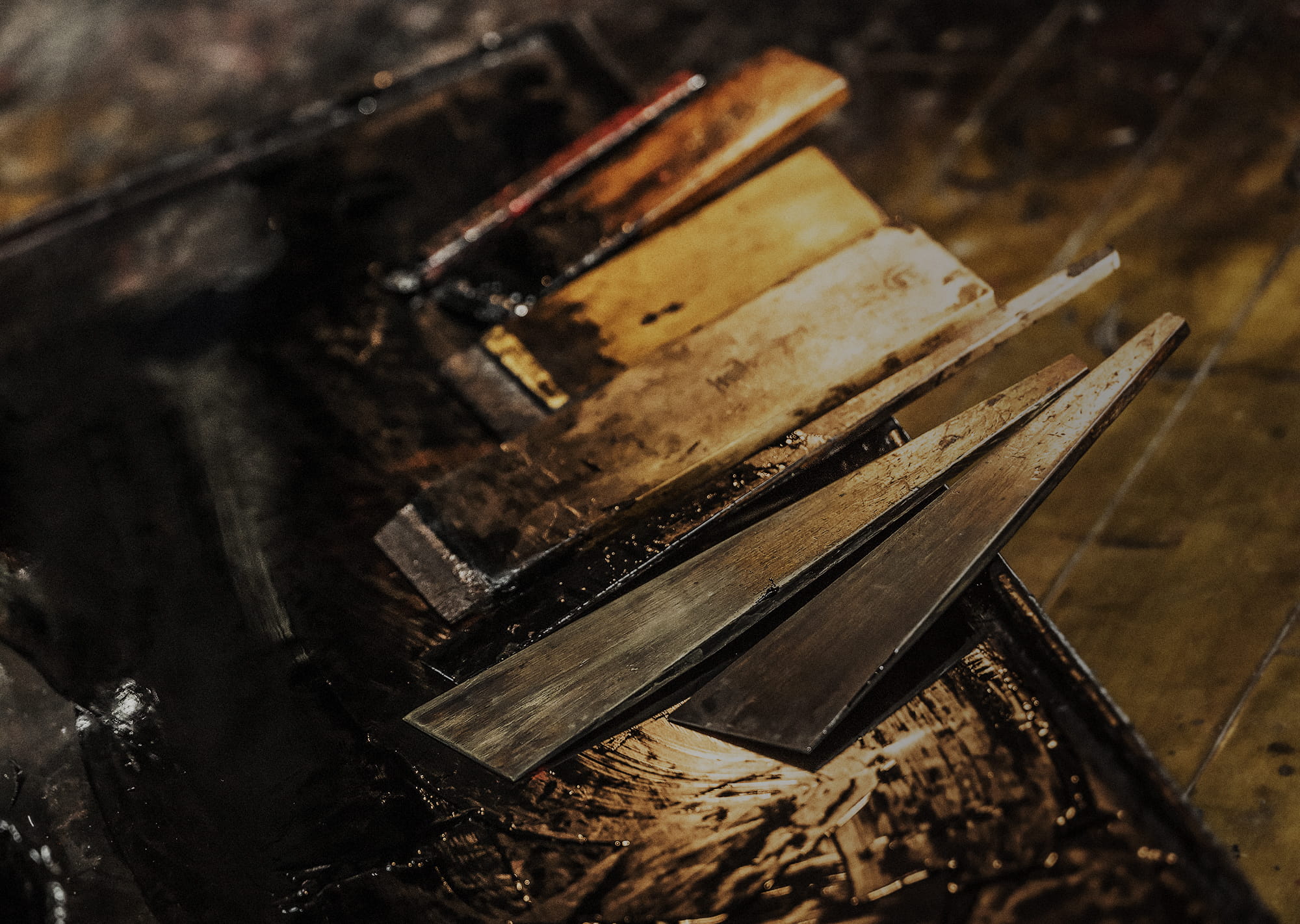
Urushi Lacquer Painter
Nu-shi
Work of urushi lacquer painter
Indispensable technique for Japanese crafts
- Introduction
-
List of Artisans
- Altar Hall Specialist(Kuden-shi)
- Woodworking Craftsman(Kiji-shi)
- Woodcarver(Hori-shi)
- Urushi Lacquer Painter(Nu-shi)
- Roiro Finish Polisher(Roiro-shi)
- Gold Leaf Craftsmen(Hakuoshi-shi)
- Colorist(Saishiki-shi)
- Makie Master(Makie-shi)
- Buddhist Sculptor(Bus-shi)
- Kirikane Gold Cutter(Kirikane-shi)
- Decorative Metalsmith(Kazarikanagu-shi)
- Gold Engraver(Chokin-shi)
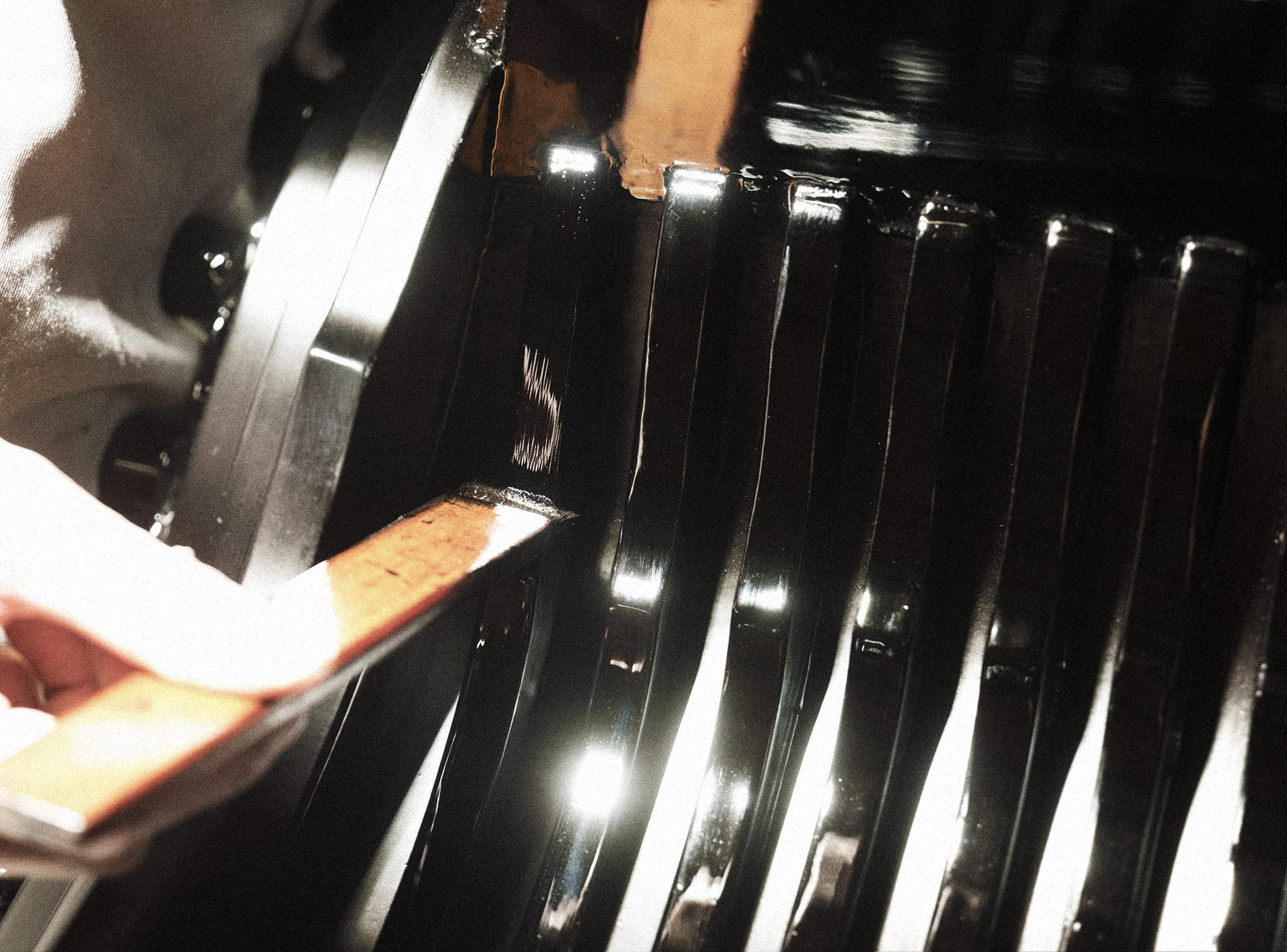
Numerous invisible works
The work of the urushi lacquerer (Nushi) begins when the wood joinery work arrives from the woodworking craftsmen. The first thing a Nushi does is to assess the condition of the woodwork. If there are any defects, they fix them. Then they coat the base with lacquer in a process called kataji or handaji. Japanese washi paper or cloth is used to strengthen the wood joinery and make the surface strong and smooth. They polish and lacquer the surface again and again.
Then they proceed to the middle coat. The lacquering and polishing process is repeated here and completed with a top coat. The top coat influences the expression and texture of the final product, so it may be coated two or three times, depending on the product. When it comes to urushi lacquer, we tend to think of the glossy surface and jet-black color. But behind it, the long work process is hidden.
Lacquerware has remained in many parts of Japan as a cultural asset since ancient times because these hidden processes play a role in both the strength and beauty of the product. The beautiful surface of lacquer and the many jobs that lie behind it. Only with this work does the lacquer shine more lustrously.
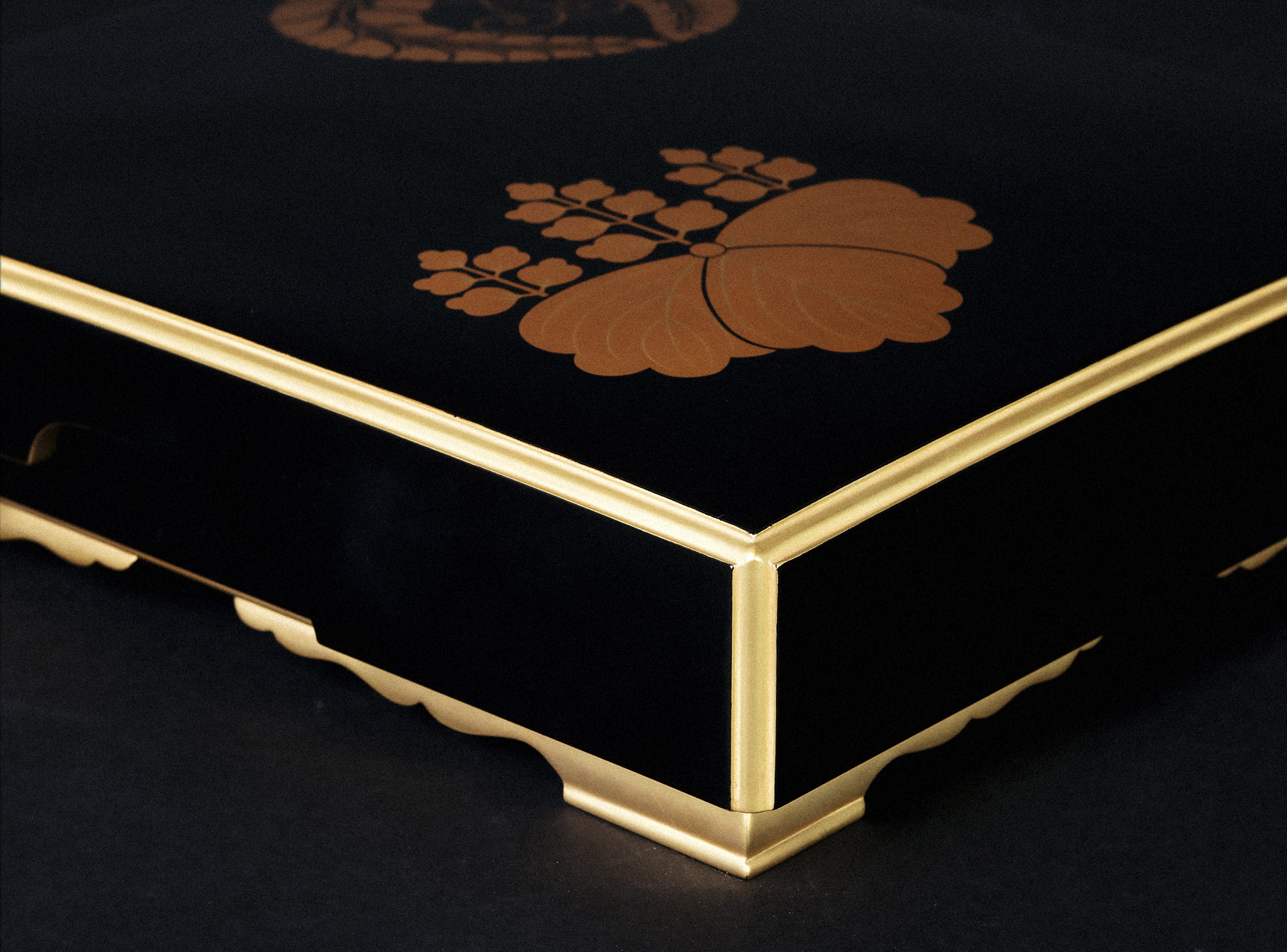
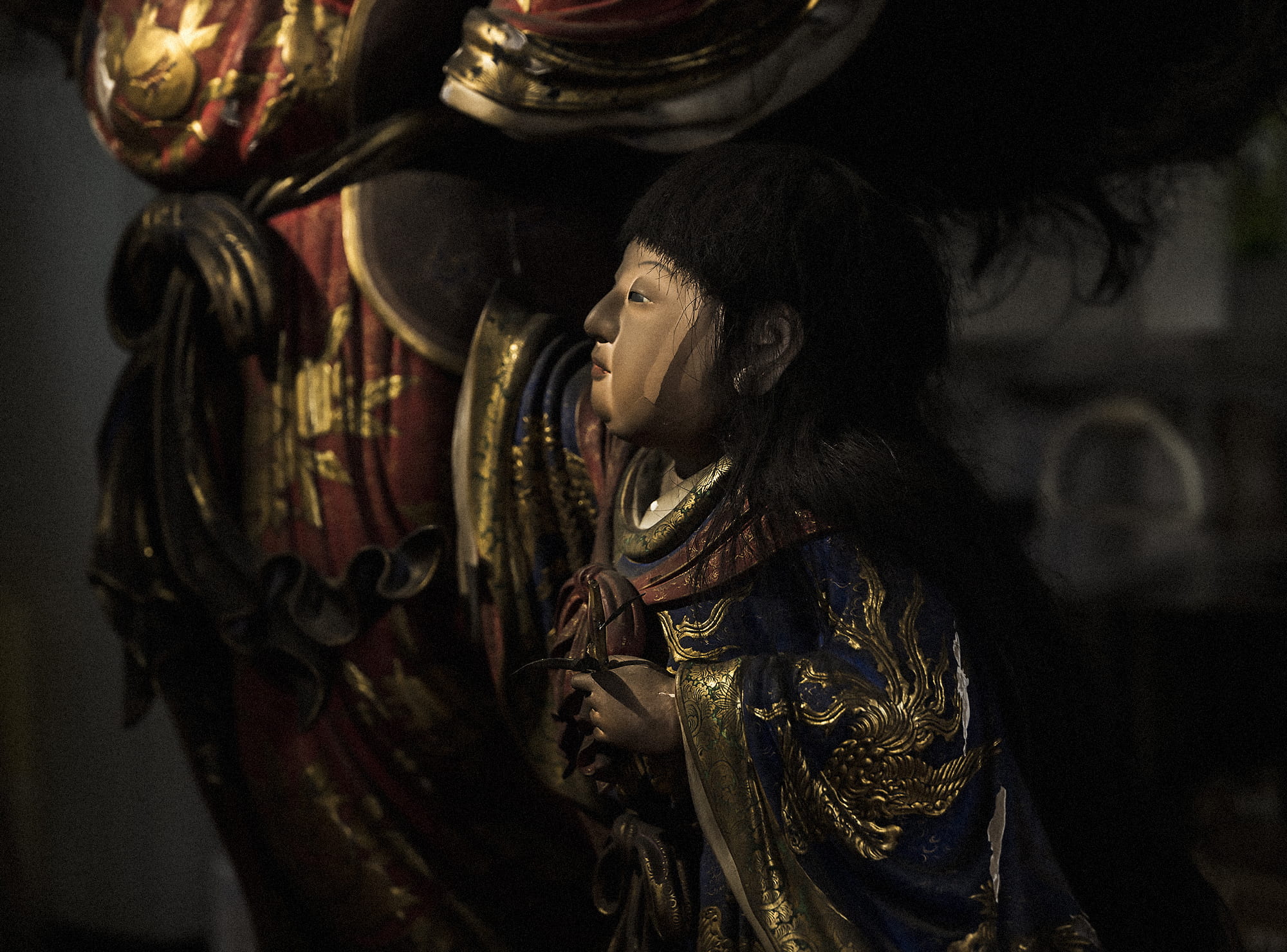
Why it's been used for so long
Urushi lacquer products have been found in the treasure room of the Shosoin (around the 8th century A.D.) and at much older sites such as the Jomon period (between c. 14,000 and 300 BC). Why is there so much urushi lacquerware? It is because of the characteristics of urushi as a material.
Urushi lacquer is waterproof, insect-proof, antibacterial, heat resistant, and strong. It also acts as a glue and effectively strengthens woodwork. For these reasons, various urushi products, not only woodwork but also impregnated fabrics have been found.
Ruins can sometimes be submerged in water. Unlike stone ruins in drier climates like Europe or Africa, the qualities of urushi lacquer play an extremely important role in preserving ancient wooden and fabric works of excellent cultural value in Japan, where humidity is high. For thousands of years, urushi lacquer has been used, tried and tested in everyday life.
Not only the surface paint, but every proccess holds a deep meaning. Just as the urushi lacquer creates layers from the base, so does its history.
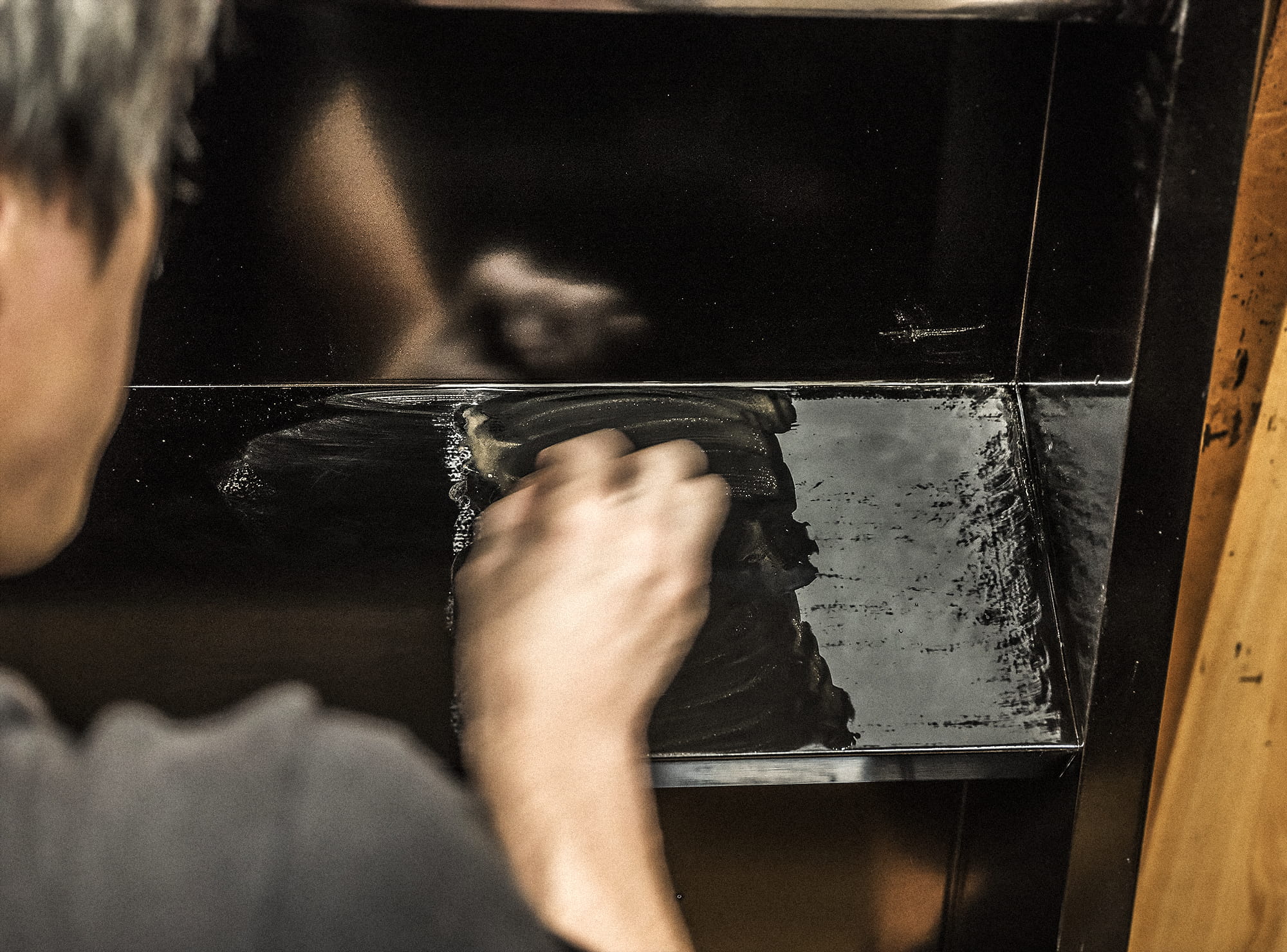
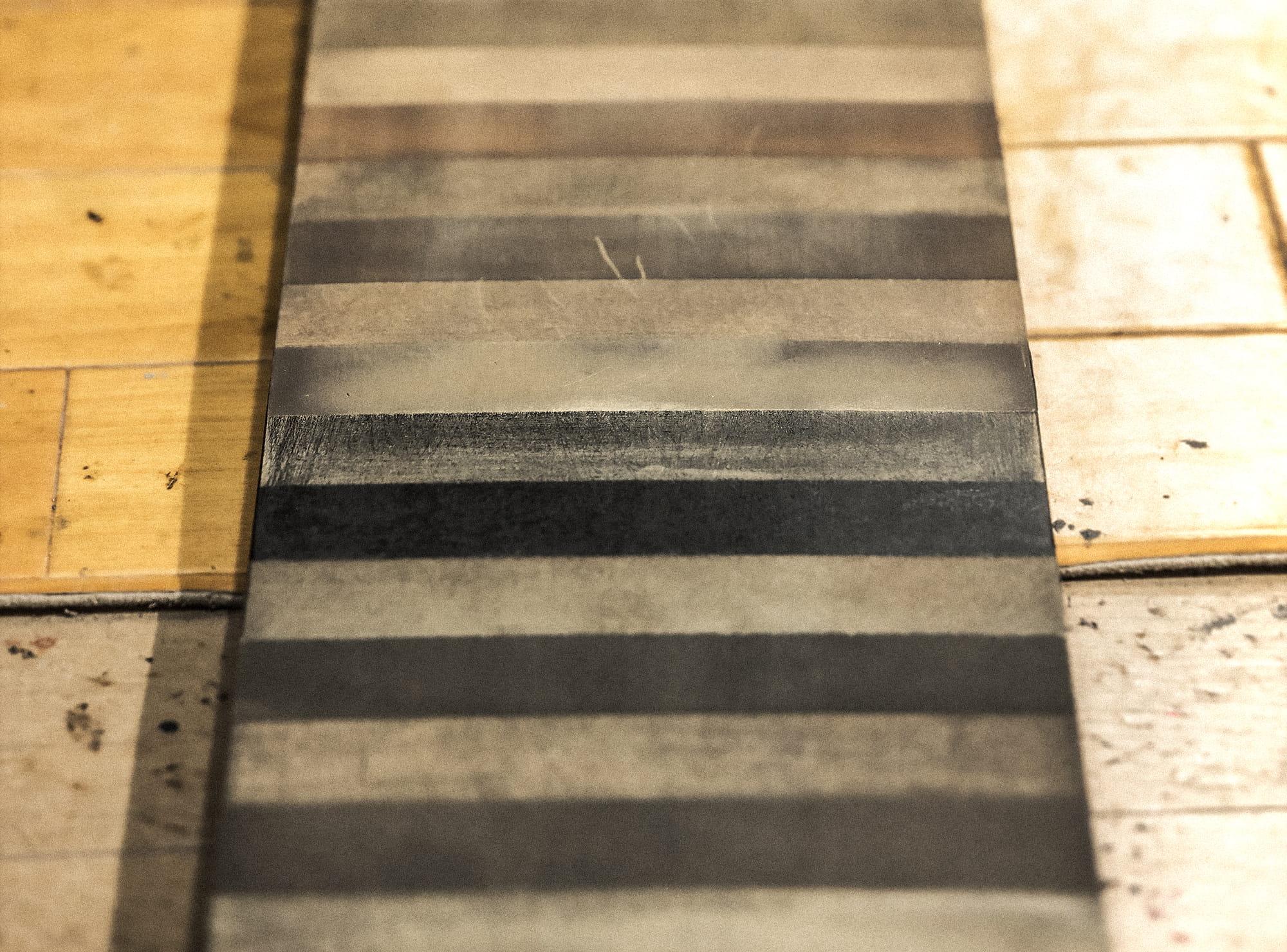
The unique expression of urushi lacquer and its texture
When you think of the color of urushi lacquer, many people think of ‘black’. Black, red, and brown are typical and unique urushi colors and have been used for centuries.
In addition to the colors found in lacquerware, there are other special expressions that have long been loved in arts and crafts. One of the typical examples is tamenuri, a technique of applying semi-transparent suki-urushi lacquer over a vermilion lacquer surface. ‘Mokume dashinuri’ is another lacquer painting technique on wood that allows the wood grain to be seen through the brown color. There is another technique called ‘uruminuri’ which is a mixture of semi-transparent urushi lacquer and red iron oxide.
And there is kanshitsu, a dry lacquer technique that gives the urushi an expression of texture. In this technique, they apply a layer of urushi lacquer on a surface such as glass, peel it off, grind it into a powder, and sprinkle it on the painted urushi surface. The end result is a gritty surface. By applying a top coat of lacquer to the surface, grinding it down, and finishing it with a final layer of urushi, it gives a gritty texture different to that of the mirrored surface. It is also possible to make various surface textures such a matte finish instead of a glossy finish. It may seem like there is only one black urushi color, but in fact there are various colors and expressive art techniques.
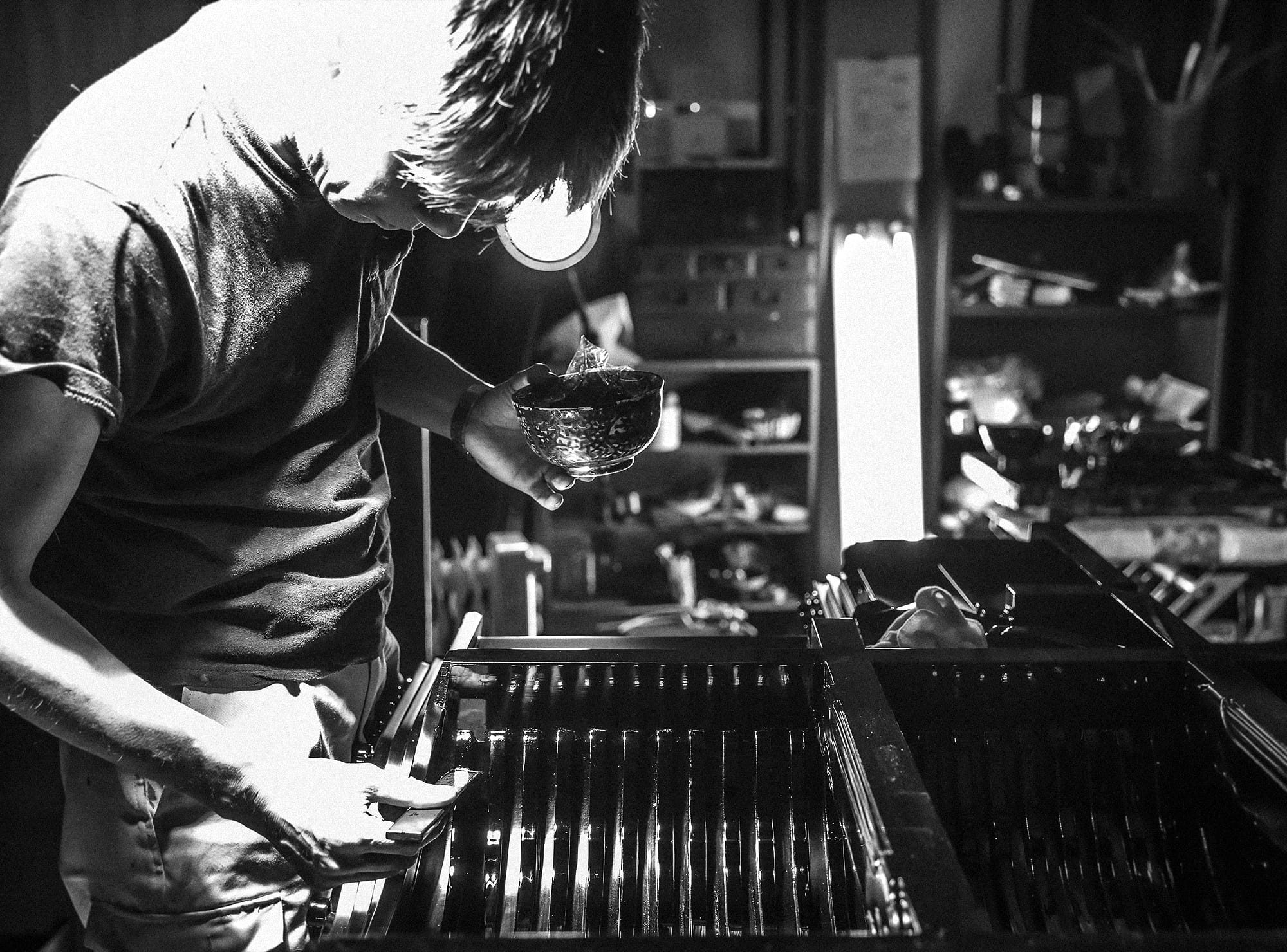