A Kudenshi is a specialist who produces the woodwork of the sacred inner main hall at the center of the temple. The main hall enshrines a Buddha image, a dais, and miniature shrines, with the founders of the particular Buddhist school enshrined on either side.
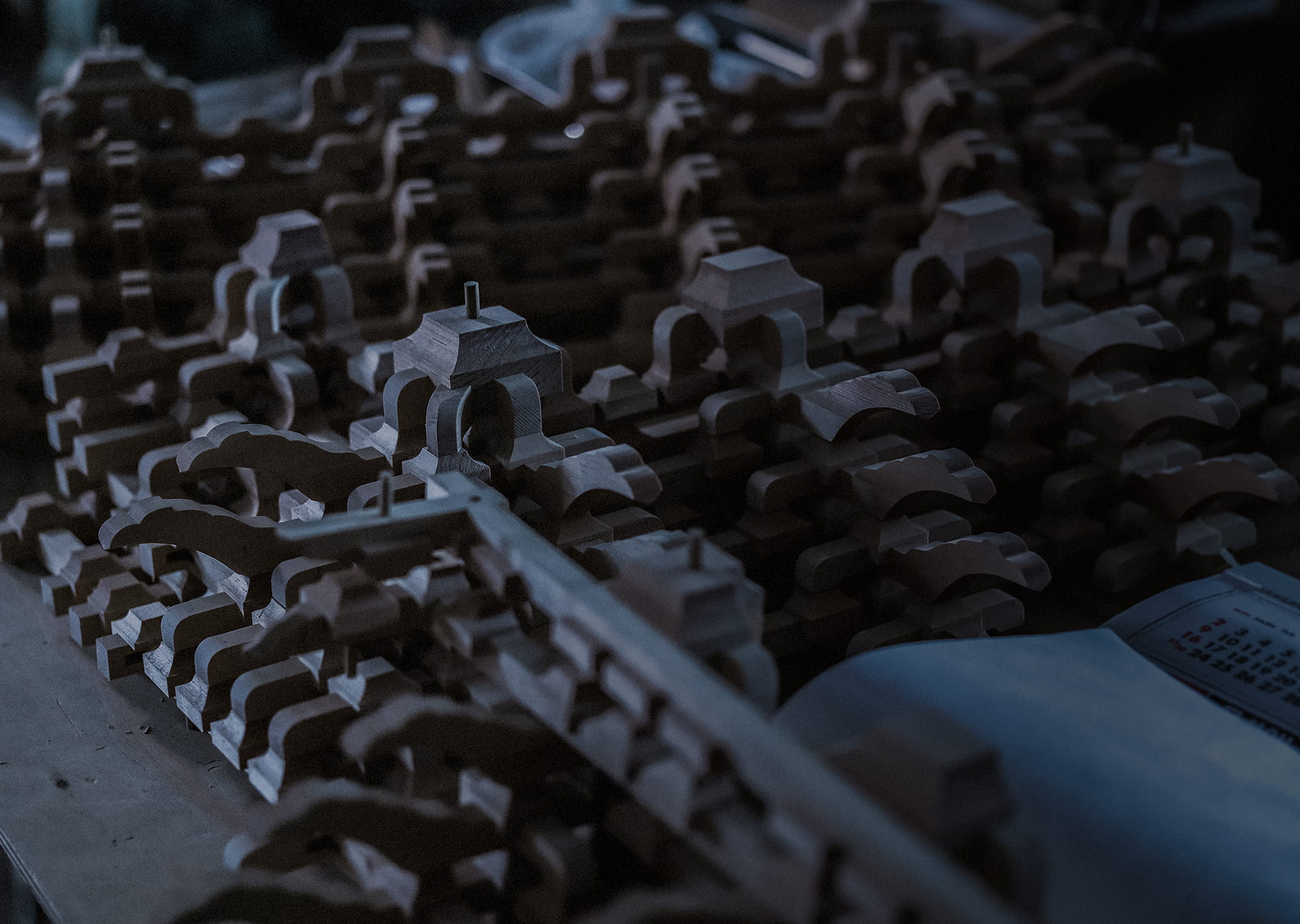
Altar Hall Specialist
Kuden-shi
Work of a Kudenshi,
an altar hall specialist
Formative arts that constitute the core of temples and shrines
- Introduction
-
List of Artisans
- Altar Hall Specialist(Kuden-shi)
- Woodworking Craftsman(Kiji-shi)
- Woodcarver(Hori-shi)
- Urushi Lacquer Painter(Nu-shi)
- Roiro Finish Polisher(Roiro-shi)
- Gold Leaf Craftsmen(Hakuoshi-shi)
- Colorist(Saishiki-shi)
- Makie Master(Makie-shi)
- Buddhist Sculptor(Bus-shi)
- Kirikane Gold Cutter(Kirikane-shi)
- Decorative Metalsmith(Kazarikanagu-shi)
- Gold Engraver(Chokin-shi)
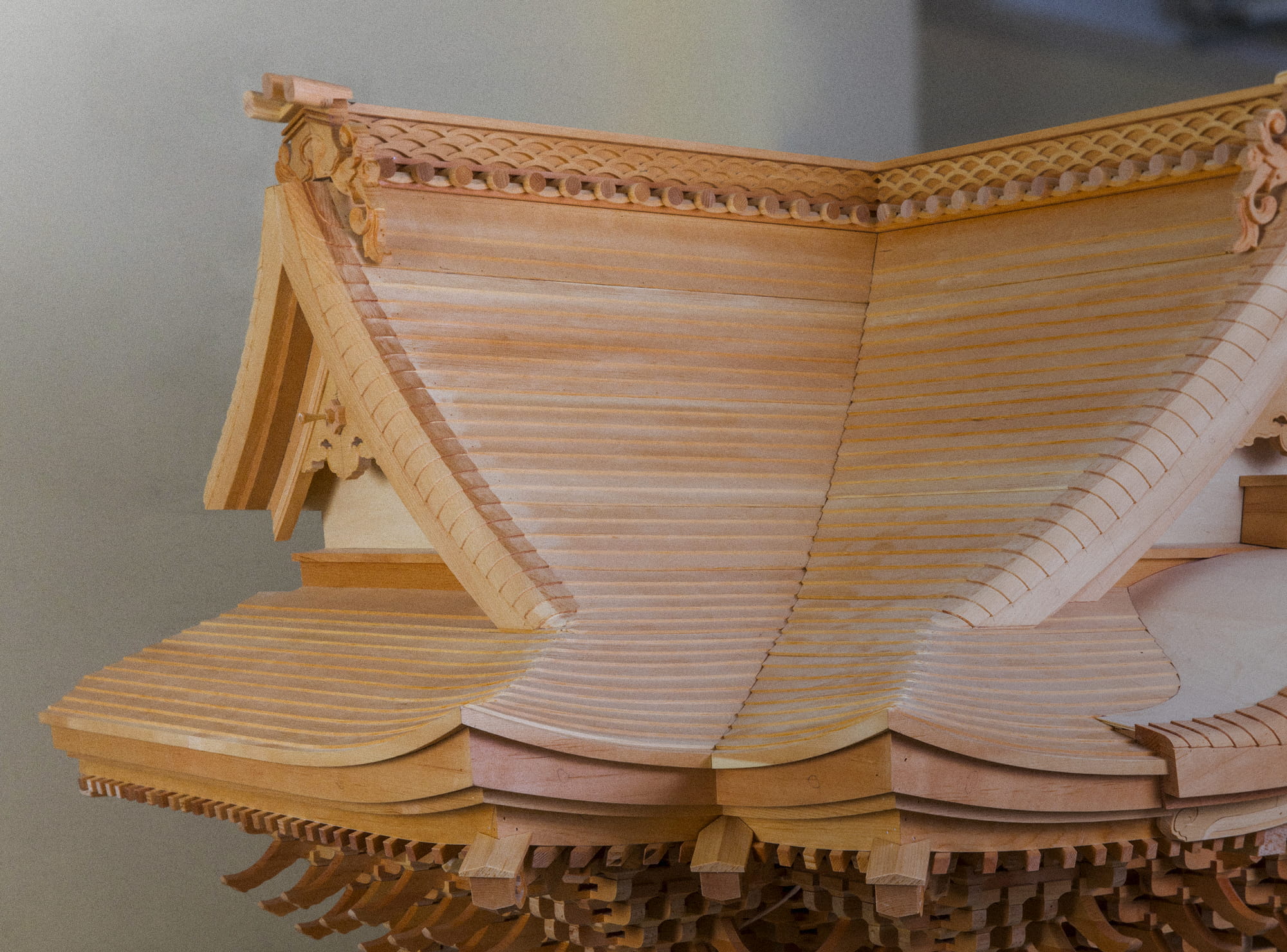
At the beginning of all work
You can’t see the altar hall specialist's work from the finished products. At the center of the temple is the Gokuden, a main hall which enshrines the principal image of worship for the denomination. The Kudenshi, altar hall specialist, produces the wooden foundation of the Gokuden.
The woodwork made by the altar hall specialist is then passed into the hands of subsequent craft workers such as the urushi lacquer painter, roiro finish polisher, gold leaf craftsman, colorist, decorative metalsmith, among others. When the product is finally completed, the woodwork cannot be seen underneath all of the ornate decorations.
Rest assured, there is superb woodwork from the artisan inside of the final product. The hall specialist determines the frame of the finished product and therefore is always aware of other artisans' work. They are mindful of how to make the work run smoothly among the artisans.
When the woodwork for the main hall is finished, you can see one- or two-millimeter gaps between the wooden joints. These gaps are used to calculate the thickness of the base coat for the urushi lacquer process that follows. When the main hall is completed, after being disassembled during each artisan's work process, the little millimeters gaps are filled in completely.
Because it is at the beginning of all work, we do not skimp on precision work, even where no one can see it.
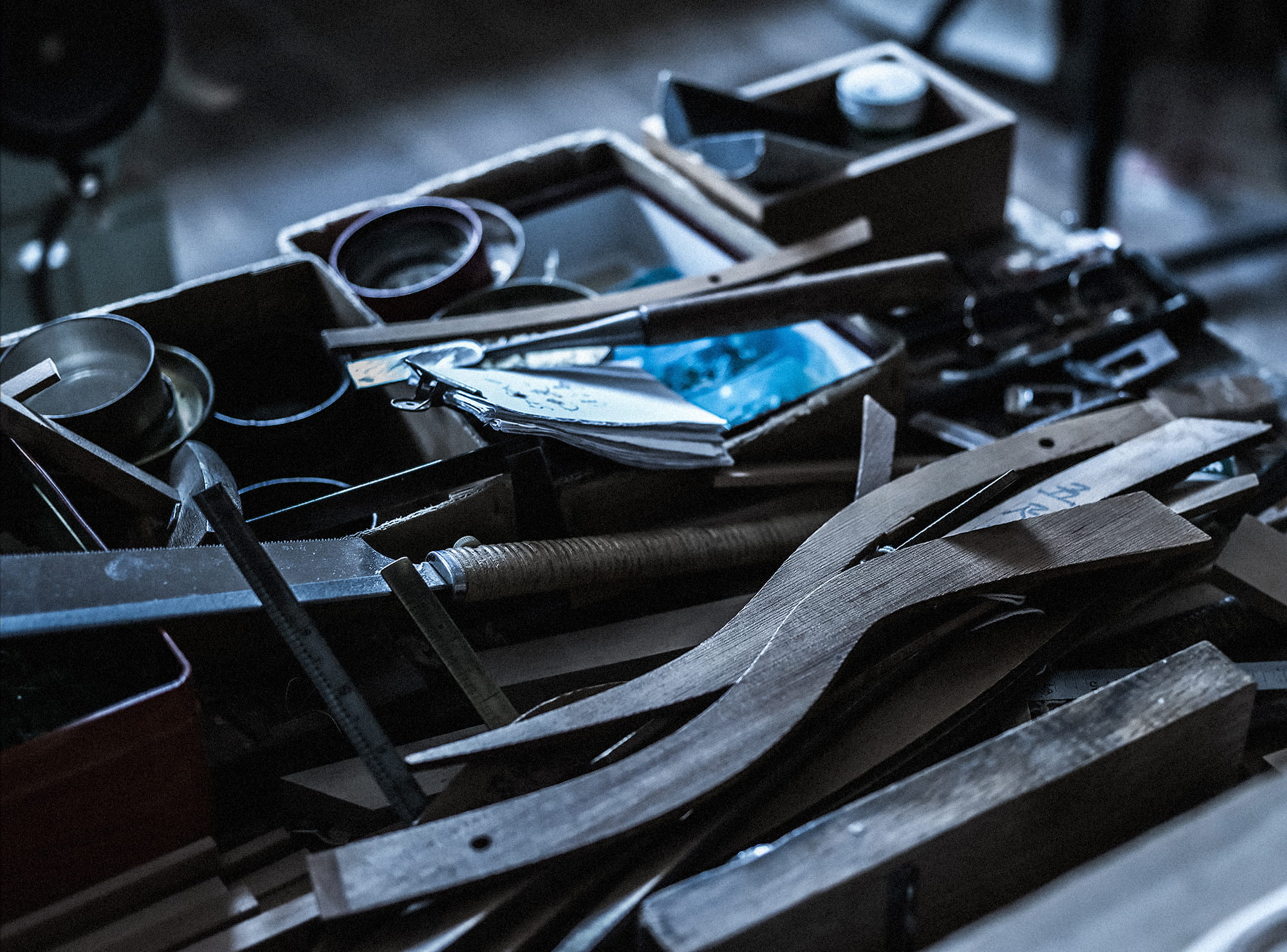
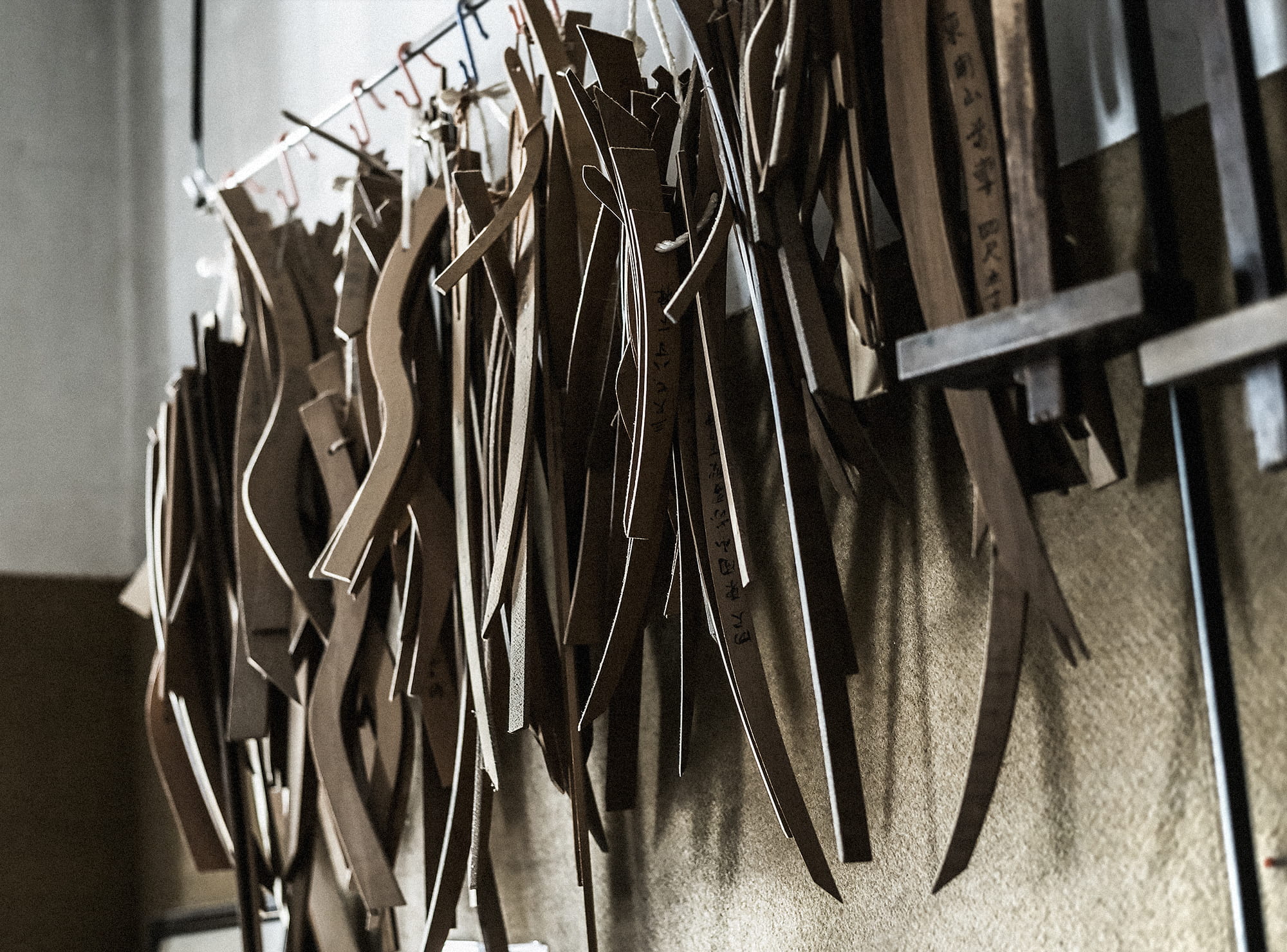
Tsue rod and Kata shape
The main hall and miniature shrine are the most architecturally-rich elements that are housed in the center of the temple. There are structures like roofs, pillars and columns, a footing foundation, square framing blocks for a screen, and a sliding door.
At present, when we work on these structures, we prepare drawings using architectural CAD, however the Kudenshi's design is preserved on two centimeters by two- or three-meter wooden rods that have the structural dimensions carved into them. This rod is called tsue. Letters and figures are written on it, which indicate the size of frontage, depth and height, making it possible to produce the entire main hall from one tsue.
Another tool that is used is called kata, a shape. These are made from wood, similar to the paper patterns used to make clothing. There are ten to fifteen kinds of kata shapes made for each tsue and they show the curved lines of the roof and the angle of the curved roof decorations.
The manufacture of the main hall starts with these two simple tools - the tsue rod and kata shapes. Over the course of time, the wisdom of these artisans has been handed down from generation to generation to create an artwork that contains a simple design, yet accumulates beauty in its decorations.
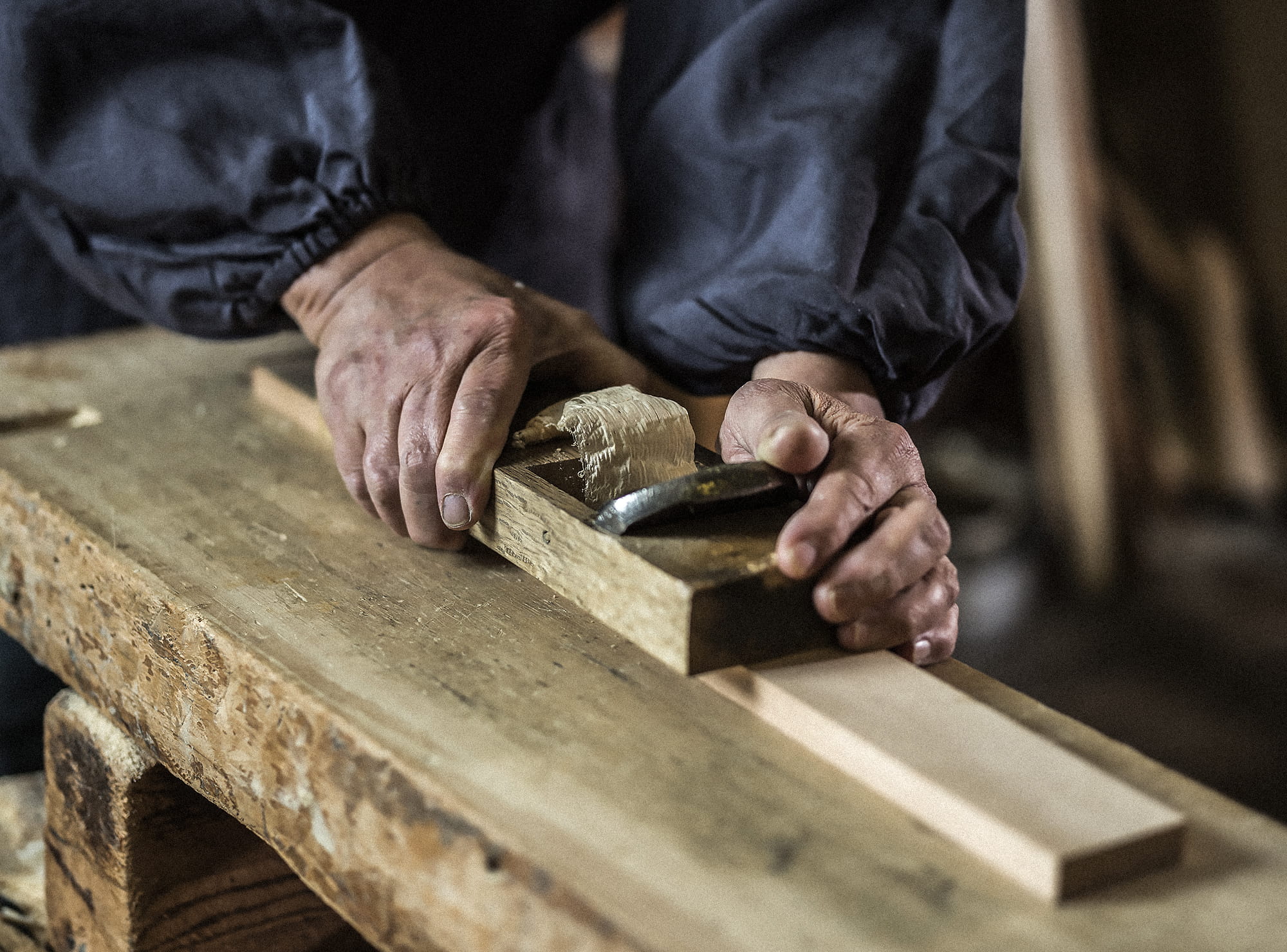
Meaning of finishing with a plane
The main tools of the Kudenshi's work are saws, chisels and planes.
The saw is used for broad shapes. The chisel creates steps and edges. And the plane smoothes everything out, including the parts that are unseen.
The Kudenshi prepares a long square piece of wood to match the diameter of a pillar. First, they shave the wood into the shape of a square, then an octagon, hexadecagon, triacontadigon and hexacontatetragon... finally, they shave alongside the grain with a plane and finish up with a circular plane. By doing this, they make the surface smooth without damaging the fiber of the wood.
This woodworking process lays the foundation for the following work that is to be done. The next step is the urushi lacquer painting. If the Kudenshi doesn't work through the entire woodworking process, minor splinters will appear in the wood, making it impossible to cover up with the thin gold leaf detail that follows. The primary work of the wood joinery is tested for the first time when seeing how the ebony urushi and gold leaf reflect light. A beautiful and delicate job is needed to pass this test. That is why the Kudenshi planes the surface of all the woodwork with pride before passing the baton to the next artisan.
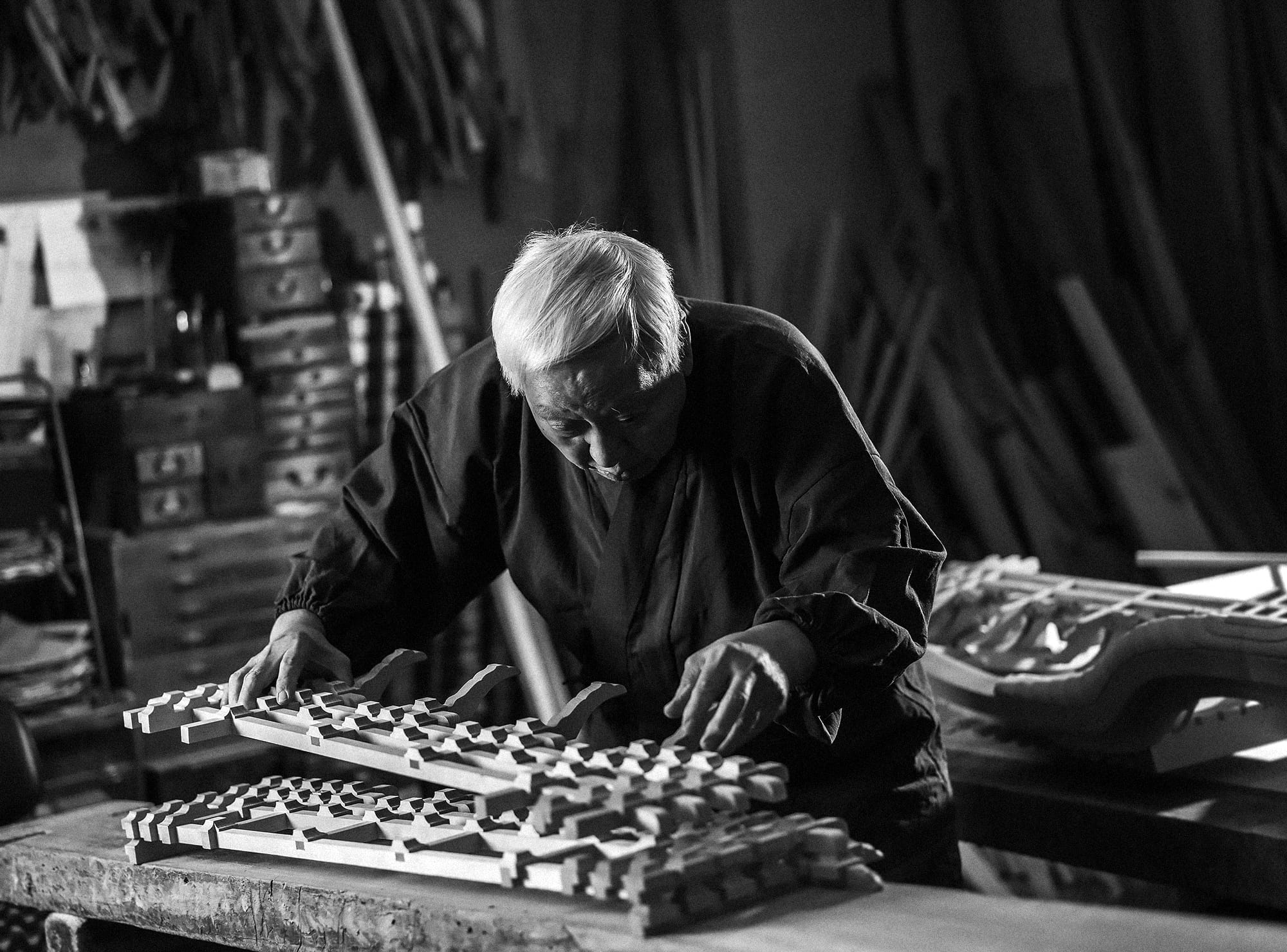